Miniaturization with geometric complexity
Nowhere is miniaturization more important than in the field of medical technology, where demand for minimally invasive treatment and ever smaller and more complex diagnostic devices is growing daily. Medical device OEMs also require increased functionality in smaller footprints.
Therefore, high-precision manufacturing technology is required that can cost-effectively produce parts and components in large quantities, regardless of the complexity of the geometry and its features, and facilitate short lead times.
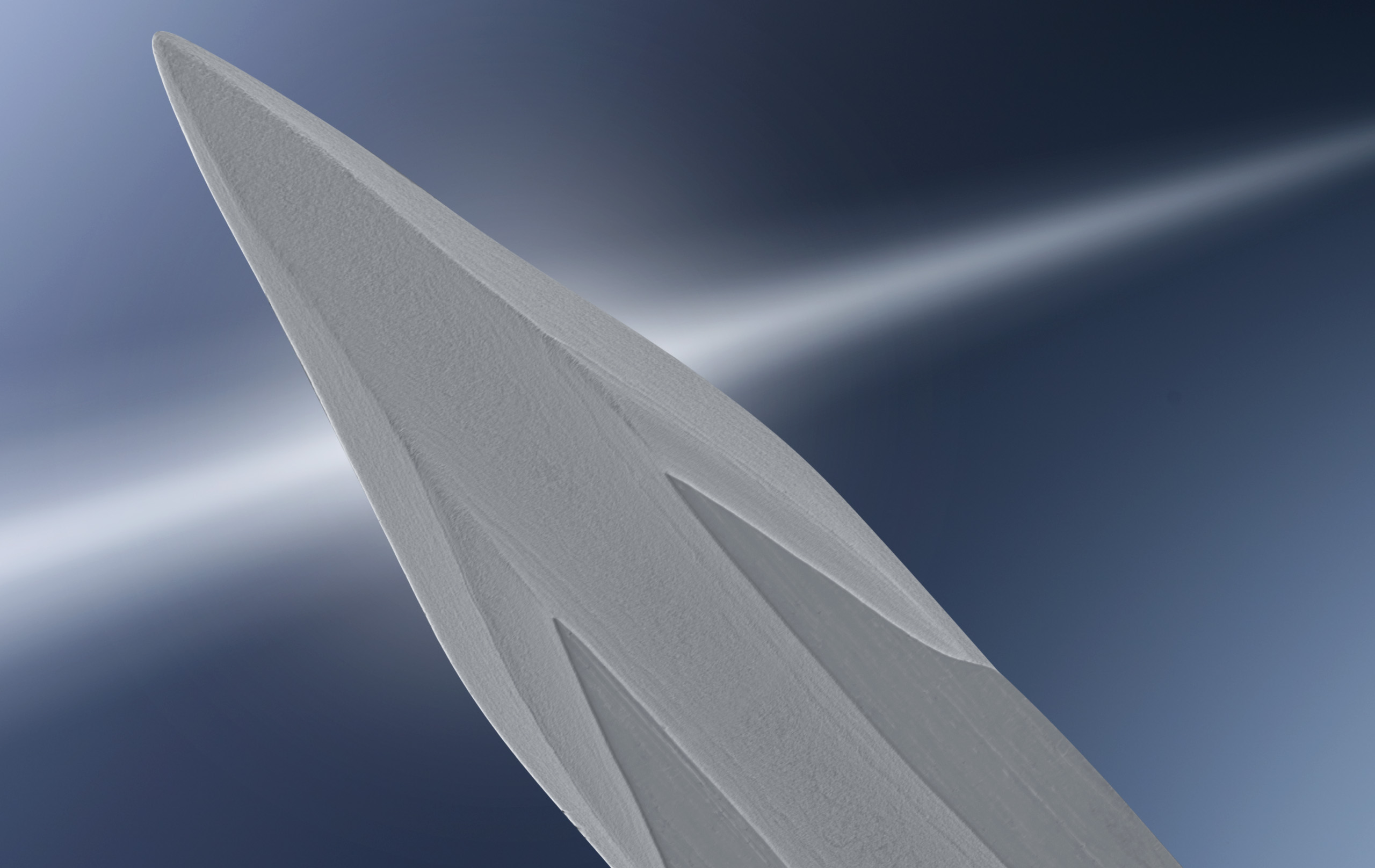
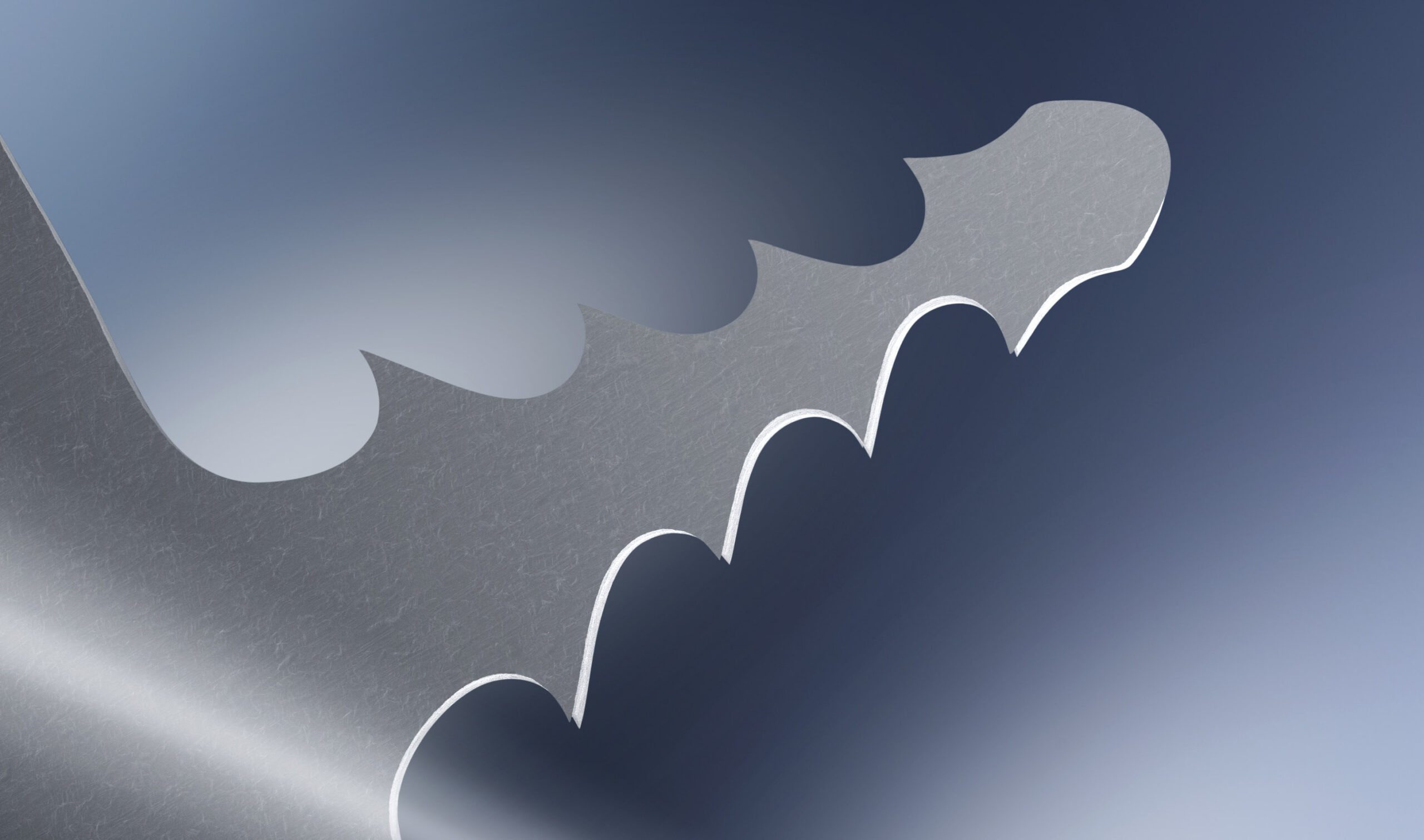
PCE for breakthrough medical devices
The photo-chemical etching process is a technological innovation that enables the design and manufacture of novel medical devices. For many medical applications, PCE is the only technology that can cost-effectively and repeatably mass produce medical devices with the stringent accuracy requirements of the medical sector.
In addition, PCE can be applied to a range of medical alloys such as titanium and nitinol. This is sometimes not possible with conventional metal processing technologies.
Advantages for medical technology
The unique properties of the PCE process make it the perfect choice for mass production of complex and feature-rich metal parts and components required by medical device OEMs. The PCE process features retention of material properties, burr- and stress-free parts with clean profiles and no heat-affected zones. This is critical when medical devices are used in safety-critical applications. The PCE process requires only easy, timely to produce, and low-cost photo tools. This shortens product development lead times and enables fast and cost-effective design adjustments. For medical device OEMs, PCE is therefore a cost-effective, highly accurate, fast, and repeatable alternative to traditional metal fabrication technologies.
Innovation is possible thanks to etching technology in medical devices that is not feasible with conventional metal fabrication technologies. A wide range of metals, even thin metal foils with a few micrometers of material thickness, can be processed using etching technology.
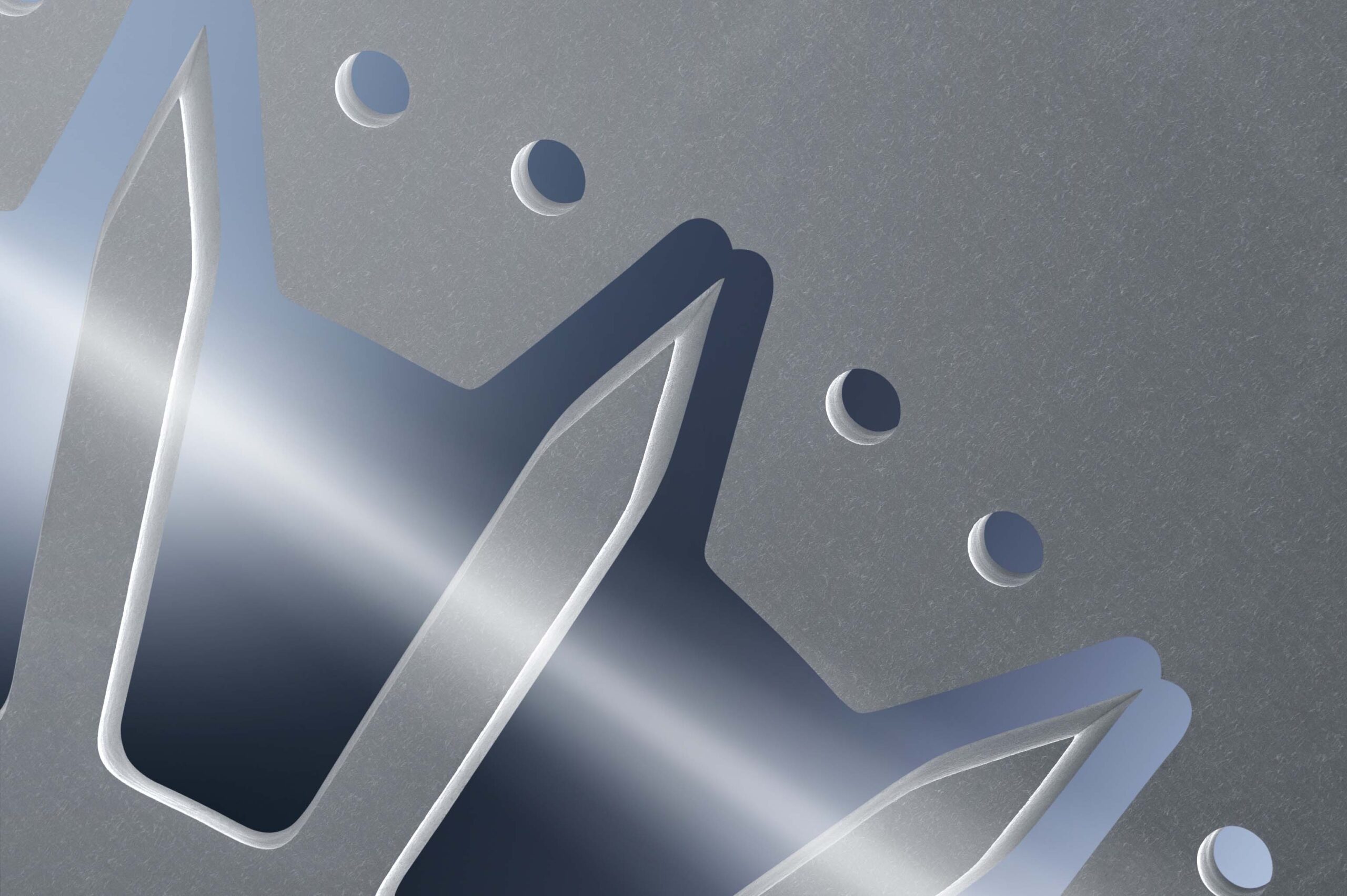
Applications
- Micro-filters
- Micro-mesh
- Medical blades
- Micro-needles
- Surgical Instruments
- Lancets
- Scalpels
- Stents
- Functional surfaces
Standards and competencies
We have a long and very successful history of working with the global medical device industry. Decades of experience with the highest standards required by medical device OEMs enables them to work with a qualified manufacturing service provider. micrometal has unparalleled knowledge in the field of PCE and the experience that comes from optimized Design for Photo Chemical Etching (DfPCE).
We are constantly adapting the proven etching process to a growing portfolio of medical metal alloys and have one of the largest etch production capacities in the world. In addition, the company offers global technical support and a range of complementary technologies to ensure that the high accuracy requirements of medical OEMs are always met.
Medicine
We can proudly announce: micrometal has been ISO 13485 certified since October 27, 2023. The international standard EN ISO 13485 is the standard for quality management systems in the medical device sector By receiving ISO 13485 certification for medical products, micrometal guarantees the highest quality and safety in the production of your etched components
micrometal's experience working with medical OEMs ensures a complete focus on the unique regulatory and standardization requirements of the medical industry, and the company is ISO 14001, ISO 9001, and IATF 16949 certified.